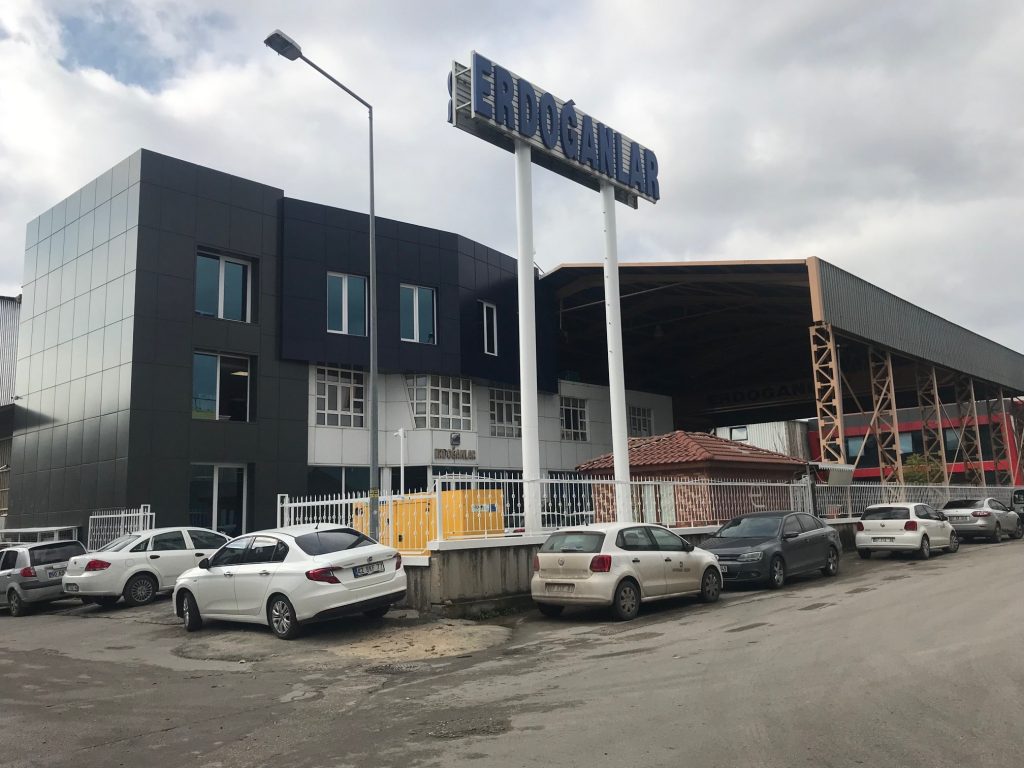
Erdoğanlar Hakkında
Erdoğanlar A.Ş. ‘nin temelleri, 1960’lı yıllarda Antalya’nın İbradı ilçesinde bakkaliye dükkanı ile atılmıştır.
1970 yılından itibaren aile, Konya’ nın Beyşehir ilçesinde ticari faaliyetlerini sürdürmüş 1990 yılında ise Erdoğanlar Ltd. Şti. olarak hem Konya hem de Antalya bölgesinde ticari hayatına devam etmiştir.2019 yılında grubumuzun büyümesiyle birlikte Anonim Şirket ünvanına geçen şirketimiz geleceğe daha büyük bir pencereden bakmaktadır.